Pumpscart is a trusted and leading provider of specialized pumps tailored to meet the unique demands of the textile industry in India. With a deep understanding of the intricacies involved in textile manufacturing, we offer a wide range of precision-engineered pumps designed to ensure efficiency, reliability, and consistency in every step of the textile production process. Our pumps are specifically crafted to handle the challenges of transferring highly viscous media, such as molasses, syrup melt, magma, mud, and massecuite, which are integral to the production of textiles. They play a critical role in facilitating the extraction and processing of materials needed for the creation of textiles, ensuring that the end products meet the highest quality standards.

Centrifugal Pumps
Centrifugal pumps are widely used for transferring water, chemicals, and dyes in textile processing. They operate by converting mechanical energy into kinetic energy to move fluids.
General Specs: Materials compatible with textile dyes and chemicals, corrosion-resistant coatings, and efficient flow rates to meet production needs.

Positive Displacement Pumps (Progressive Cavity Pumps)
Progressive cavity pumps are excellent for handling shear-sensitive fluids and viscous materials used in textile dyeing and finishing processes.
General Specs: Progressive cavity design for gentle, consistent flow, and materials suitable for textile chemicals.

Diaphragm Pumps
Diaphragm pumps are chosen for their ability to handle abrasive and chemically aggressive fluids commonly found in textile production.
General Specs: Sealless design, chemical-resistant materials, and robust diaphragms for durability.

Peristaltic Pumps
Peristaltic pumps are ideal for metering and dosing tasks in textile dyeing. They provide accurate and gentle handling of dyes and chemicals.
General Specs: Tubing materials compatible with dyes, precise dosing capabilities, and easy maintenance.

Air-Operated Double Diaphragm (AODD) Pumps
AODD pumps are versatile and can handle a range of textile chemicals, including solvents, dyes, and finishings, making them essential in textile processing.
General Specs: Sealless operation, chemical compatibility, and suitability for various chemical viscosities.

Gear Pumps
Gear pumps are used for transferring oils and lubricants for textile machinery maintenance. They provide a consistent and controlled flow.
General Specs: Materials compatible with oils and lubricants, precision engineering for accuracy, and minimal pulsation.

Lobe Pumps
Lobe pumps are preferred for handling shear-sensitive materials and dyes in textile applications while maintaining product quality.
General Specs: Hygienic design, low shear action, and materials compatible with textile chemicals.

High-Pressure Pumps
High-pressure pumps are essential for certain textile processes requiring pressurized water, such as fabric finishing and dye fixation.
General Specs: Ability to generate and maintain high pressure, materials suitable for textile chemicals, and efficiency in high-pressure applications.
Certainly, here are a few more types of pumps used in the textile industry, along with their descriptions and general specifications:

Submersible Pumps
Submersible pumps are employed for draining water from dyeing and washing machines in textile processing. They are designed to operate underwater without risk of electrical hazards.
General Specs: Submersible and water-resistant design, corrosion-resistant materials, and efficient water handling.

Self-Priming Pumps
Self-priming pumps are utilized for processes that require pumps to maintain prime and create a vacuum, such as transferring dyes and chemicals.
General Specs: Ability to self-prime, compatibility with textile chemicals, and efficient priming and pumping.

Centrifugal Immersion Pumps
Centrifugal immersion pumps are submerged directly into processing tanks and are suitable for circulating and agitating dye baths and chemicals.
General Specs: Submersible design, corrosion-resistant materials, and ability to handle agitated solutions.

Vertical Turbine Pumps
Vertical turbine pumps are employed for lifting and transferring water from wells and reservoirs used in textile facilities for various applications.
General Specs: Long pump life, vertical design for space efficiency, and materials suitable for water handling.
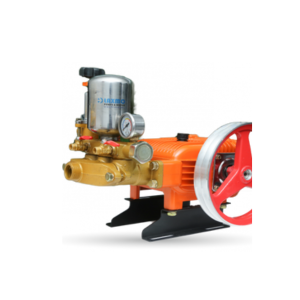
Piston Pumps
Piston pumps are used for precision dosing and high-pressure tasks, such as applying finishing chemicals or dyes to textiles.
General Specs: High-pressure capabilities, precise dosing, and compatibility with textile chemicals.
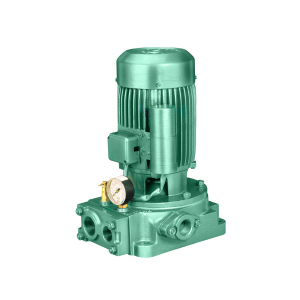
Jet Pumps
Jet pumps are used for the transfer of water and chemicals in textile facilities, offering a simple and cost-effective solution for fluid movement.
General Specs: Simple and efficient design, compatibility with water and chemicals, and low maintenance requirements.

Multistage Pumps
Multistage pumps are essential for applications requiring high-pressure water or chemical transfer, such as high-pressure dye application.
General Specs: Ability to generate and maintain high pressure, corrosion-resistant materials, and durability in high-pressure environments.
Certainly, here are a few more types of pumps used in the textile industry, along with their descriptions and general specifications:

Syringe Pumps
Syringe pumps are employed for precise and controlled injection of small volumes of dyes and chemicals in textile laboratories and small-scale dyeing processes.
General Specs: High precision and accuracy, compatibility with a range of chemicals, and compact design.

Sump Pumps
Sump pumps are used to remove accumulated water and liquids from sumps and basements in textile facilities, helping to prevent flooding and water damage.
General Specs: Submersible and water-resistant design, efficient water removal, and durability.

Explosion-Proof Pumps
Explosion-proof pumps are required in hazardous areas of textile facilities where flammable materials or environments are present, ensuring safety during fluid transfer.
General Specs: Compliance with explosion-proof standards, robust construction, and compatibility with various fluids.

Vertical Inline Pumps
Vertical inline pumps are used for circulating water, chemicals, and coolants in textile equipment and systems, offering space-saving installation.
General Specs: Vertical design for space efficiency, corrosion-resistant materials, and reliability in continuous operation.

Chemical Dosing Pumps
Chemical dosing pumps are employed for precise injection of chemicals in textile processes, helping to maintain consistent chemical concentrations.
General Specs: Precise dosing capabilities, compatibility with various textile chemicals, and reliability.
Applications of Pumps in the Textile Industry:
1. Dyeing and Coloring: Pumps play a crucial role in the transfer and circulation of dyes and colorants, ensuring even color distribution in textiles.
2. Chemical Handling: Pumps are used for the precise dosing and transfer of chemicals required for processes like pretreatment, finishing, and printing.
3. Water Management: Pumps are essential for handling water in textile manufacturing, including drainage, circulation, and supply to various processes.
4. High-Pressure Dye Application: High-pressure pumps are used for applying dyes to textiles, ensuring deep and consistent color penetration.
5. Liquid Waste Management: Pumps help in the removal and disposal of liquid waste and effluents generated during the textile production process.
6. Circulation in Machines: Textile machines, such as dyeing machines, rely on pumps for efficient circulation of liquids within the equipment.
7. Cooling and Lubrication: Pumps are used to provide cooling and lubrication to textile machinery, enhancing their operational efficiency.
Technological Advancements and Innovations:
1. Smart Pumping Systems: Integration of sensors and automation for real-time monitoring and control of pump performance, optimizing efficiency.
2. Energy-Efficient Pumps: Advanced designs and the use of variable frequency drives (VFDs) to reduce energy consumption and operational costs.
3. Sealless Pump Technologies: Innovations in sealless designs, such as magnetic drives, improve safety and reduce the risk of leaks in chemical handling.
4. Remote Monitoring: The use of IoT (Internet of Things) for remote monitoring of pump performance, enabling predictive maintenance and minimizing downtime.
5. Hygienic Pump Design: Hygienic pumps with polished surfaces, easy disassembly for cleaning, and compliance with food safety standards for textile processes involving food-grade materials.
6. Precision Dosing: Innovative dosing pumps with high precision capabilities for accurate chemical dosing in textile treatments.
Challenges and Solutions:
1. Chemical Compatibility: Textile processes involve various chemicals, and choosing pumps compatible with these chemicals is crucial to prevent corrosion and ensure longevity. Solution: Select pumps with materials suitable for specific chemicals.
2. Maintenance and Cleanability: Maintaining pump hygiene and cleanability in the textile industry is essential to prevent contamination. Solution: Opt for pumps with easy disassembly and cleaning features.
3. Energy Consumption: High energy consumption is a concern in the textile industry. Solution: Use energy-efficient pump designs and implement VFDs to optimize energy use.
4. High-Pressure Requirements: High-pressure dye application demands specialized pumps. Solution: Choose pumps designed to generate and maintain high pressure for consistent and deep color penetration.
5. Shear-Sensitive Products: Gentle handling is crucial for shear-sensitive textile materials. Solution: Select pumps like peristaltic and lobe pumps designed for gentle product transfer.
6. Water Management: Efficient water circulation and management are essential. Solution: Employ pumps for water supply, drainage, and circulation, ensuring water conservation and quality.
FAQ
What was commonly used in textile industry?
Cotton is one of the primary fabrics utilized in the textile industry. This means there needs to be an efficient machine that can separate the cotton fibers from the cotton seed.
What products are made in the textile industry?
Textile product mills convert raw textiles into finished products other than apparel. Some of the items made in this sector include household items, such as carpets and rugs, towels, curtains and sheets, cord and twine, furniture and automotive upholstery, and industrial belts and fire hoses.
What is the purpose of textile industry?
The textile industry is primarily concerned with the design, production and distribution of yarn, cloth and clothing. The raw material may be natural, or synthetic using products of the chemical industry.
What are the benefits of textile industry?
- Quality Improvement.
- Foreign Direct Investment (FDI) Policy.
- Abundant availability of Raw Materials.
- Low costs.
- Manufacturing flexibility.
- Lower lead times.
- Favorable demand conditions – large, growing domestic market.
- Strong presence of related and supporting industries.
Textile industrial pump specifications
What types of pumps are commonly used in the textile industry?
How do I choose the right pump for my textile application?
Selecting the right pump depends on factors like the type of fluid or chemical, required flow rate, pressure, and the specific process. Consult with pump experts to ensure compatibility.
How are pumps cleaned and maintained in the textile industry to prevent contamination?
Pumps are cleaned and maintained through a combination of manual cleaning, flushing with cleaning agents, and adhering to clean-in-place (CIP) procedures to maintain hygiene standards.
Are there energy-efficient pump options for textile facilities looking to reduce operational costs?
Yes, energy-efficient pump designs, variable frequency drives (VFDs), and the optimization of pump operation can help reduce energy consumption and operational costs.
What challenges do textile facilities face in chemical handling, and how are they addressed?
Challenges include the compatibility of pumps with various textile chemicals. Address this by selecting pumps with materials suitable for specific chemicals.
Can pumps handle shear-sensitive materials in textile dyeing and finishing?
Yes, certain pump types like peristaltic and lobe pumps are designed for gentle handling of shear-sensitive materials, preserving product quality.
How do pumps contribute to water management in textile processes?
Pumps play a significant role in water supply, drainage, and circulation, optimizing water use and ensuring efficient textile manufacturing processes.
Are there innovative technologies for pump monitoring and maintenance in textile facilities?
Yes, innovations such as smart pumping systems and remote monitoring with IoT (Internet of Things) enable real-time monitoring, predictive maintenance, and efficient management of pump performance.
What are the considerations for high-pressure dye application in textiles, and how are they met?
High-pressure pumps are used for deep and consistent color penetration. Select pumps designed to generate and maintain high pressure while being compatible with textile dyes.
How can textile facilities ensure pump hygiene and cleanability for regulatory compliance?
Choose pumps with hygienic designs, polished surfaces, and easy disassembly for cleaning, ensuring compliance with food safety and hygiene standards.